3000w 2 in 1 handheld laser welder review
3000W 2 in 1 Laser Welder technology has revolutionized the metal fabrication industry, providing a precise and efficient method for joining materials compared to traditional welding techniques. This innovative process utilizes focused laser beams to melt and fuse metal components, producing strong welds with minimal heat input. As industries continually seek advancements in manufacturing processes, laser welding has gained prominence due to its exceptional accuracy and speed.
The evolution of laser welding can be traced back to its initial development in the 1960s, when researchers began to explore the potential of lasers in industrial applications. Over the decades, advancements in laser technology, such as the introduction of fiber and diode lasers, have significantly enhanced both the quality and speed of the welding process. These modern laser systems allow for greater versatility, particularly in the fabrication of intricate components, which traditional welding methods may struggle to achieve.
Unlike conventional welding techniques, which often involve the application of filler materials and create wider heat-affected zones, laser welding concentrates energy into a small area. This results in cleaner, more precise weld seams with less distortion and post-weld processing required. Moreover, the reduced heat input decreases the likelihood of defects such as warping or cracking, making laser welding especially suitable for applications in industries where precision is critical, such as aerospace and medical device manufacturing.
Furthermore, the increasing demand for automation and efficiency in manufacturing processes has propelled the adoption of laser welding technology. The capability to integrate laser welders into automated production lines enhances productivity and consistency, ensuring high-quality results at reduced costs. As industries continue to prioritize precision and efficiency, the role of laser welding technology is expected to expand, solidifying its position as a pivotal player in modern metal fabrication.
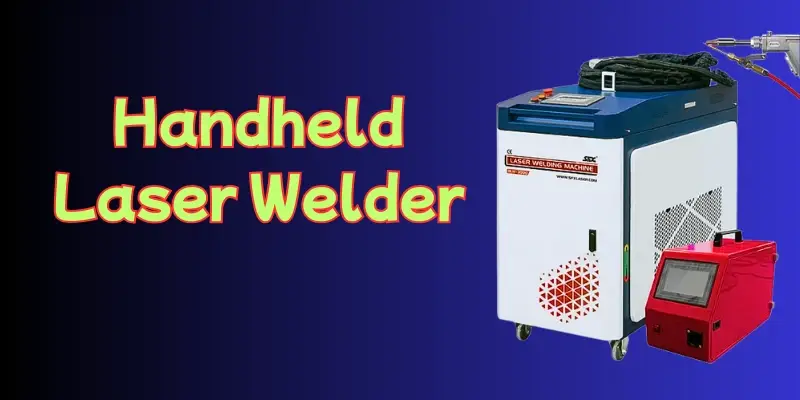
Overview of the 3000W 2 in 1 Laser Welder
The 3000W Laser Welder represents a significant advancement in metal fabrication technology, combining high power output with innovative design to enhance welding efficiency. This device is engineered for versatility, allowing its use in both welding and cutting applications, making it suitable for various materials such as stainless steel, carbon steel, and aluminum. The dual-functionality not only optimizes workflow but also saves on the need for multiple machines, which can be a considerable cost benefit in industrial settings.
One of the key specifications of this handheld laser welder is its impressive 3000W power capacity, which enables it to deliver a strong, focused beam capable of penetrating thicker materials with ease. This high wattage translates into faster welding speeds, which is essential for improving productivity in fabrication tasks. Moreover, the welder is designed with portability in mind, featuring a lightweight and ergonomic handle that facilitates ease of use during prolonged operation.
Operating the 3000W 2-in-1 laser welder is straightforward, thanks to its user-friendly interface and intuitive controls. Weld settings can be easily adjusted to suit specific material thicknesses and types, enabling users to achieve optimal results consistently. The precision of the laser beam also minimizes heat-affected zones, which is critical in preventing distortion in the workpiece. This makes the welder particularly advantageous in applications that require meticulous finishes and structural integrity.
In summary, the 3000W 2 in 1 Laser Welder combines power, flexibility, and ease of use, making it a valuable addition to any metal fabrication workshop. Its ability to perform both welding and cutting operations positions it as a key tool for professionals seeking reliability and efficiency in their projects.
Key Features of the 3000W 2 in 1 Laser Welder
The 3000W 2 in 1 Laser Welder is engineered with several standout features that not only enhance usability but significantly improve efficiency in metal fabrication. One of the most notable features is the integrated auto wire feeder, which streamlines the welding process. This automatic mechanism reduces the need for manual wire loading, thereby minimizing downtime and allowing for continuous operation. It ensures that the correct amount of filler material is dispensed during the welding process, significantly increasing the quality of the weld and reducing waste.
Another remarkable attribute of the 3000W 2 in 1 Laser Welder is its handheld design. This ergonomic feature offers operators flexibility and maneuverability, allowing them to perform intricate welding tasks in hard-to-reach areas without the constraints of traditional welding machines. The lightweight structure provides ease of handling, which is essential for both professional welders and those engaged in DIY projects. This adaptability makes it suitable for various applications, from industrial settings to home workshops.
The welder’s capability to work with multiple types of metals further enhances its functionality. It is adept at welding carbon steel, stainless steel, aluminum, and even titanium, making it an invaluable tool for a diverse range of projects. This versatility broadens its usability across different industries, including automotive, aerospace, and construction, where different metals often require precise welding techniques. The 3000W laser welder facilitates quick adjustments to settings, which ensures that welders can optimize their parameters based on the material being worked on.
In summary, the 3000W handheld laser welder, with its auto wire feeder, ergonomic design, and multi-metal capabilities, is a revolutionary tool in the metal fabrication sector that promises to increase productivity and efficiency across various applications.
Advantages of Using a 3000W 2 in 1 Laser Welder
The introduction of the 3000W 2-in-1 handheld laser welder represents a significant advancement in the field of metal fabrication. One of the primary benefits of utilizing this type of welding technology is the reduction of the heat-affected zone (HAZ). Unlike traditional welding methods, which often generate excessive heat, the laser welder focuses energy precisely on the weld area. This concentrated heat minimizes thermal distortion, ensuring that nearby metal remains unaffected. Consequently, this leads to a higher quality of welds with reduced warping and fewer complications in the overall assembly process.
In addition to improved weld quality, the handheld laser welder boasts faster processing times. The efficiency of a 3000W laser welder allows for rapid welding without compromising the integrity of the workpiece. This increased speed is particularly advantageous in high-volume manufacturing settings where time translates to cost-effectiveness. As operations can be completed more quickly, businesses can expect improved throughput and enhanced productivity, ultimately leading to a more competitive edge in the market.
Moreover, operational costs can significantly decrease when employing a 3000W 2 in 1 Laser Welder. The precision offered by this technology means less filler material is utilized, as the need for additional welding passes is reduced. Additionally, the low maintenance requirements of laser equipment result in fewer downtimes and less expenditure on repairs and maintenance. These factors combined can lead to substantial savings over the equipment’s lifespan, which can facilitate reinvestment in further technological advancements or additional resources.
Lastly, the versatility of the 2-in-1 feature allows users to switch between welding and cutting tasks seamlessly, further enhancing the utility and cost-effectiveness of this advanced welding solution. In summary, the advantages of using a 3000W laser welder dramatically enhance the capabilities of metal fabrication, making it a viable choice for modern manufacturing processes.
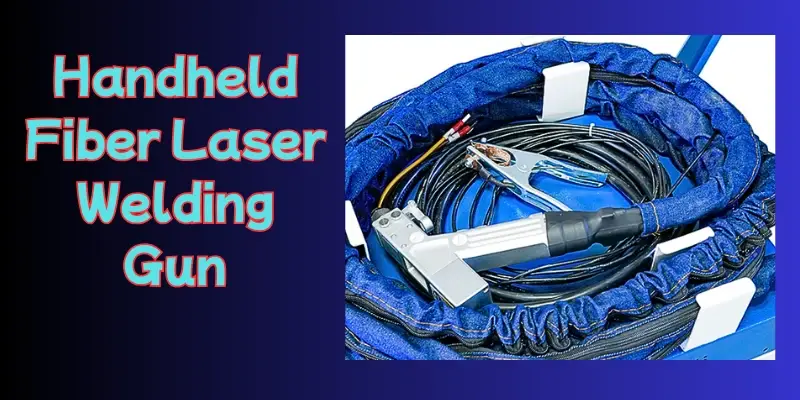
Applications of the Handheld Laser Welder
The 3000W handheld laser welder represents a significant innovation in the field of metal fabrication, with a remarkable breadth of applications across various industries. One of the most prominent sectors benefiting from this technology is the automotive industry. With the capability to perform precision welding on diverse materials such as aluminum, stainless steel, and carbon steel, this tool is invaluable for manufacturers and repair shops. It allows for intricate joint designs which enhance both the strength and aesthetics of automotive components, facilitating streamlined production processes and reducing costs associated with traditional welding methods.
Aerospace is another critical industry that sees substantial advantages from the use of this handheld laser welder. The lightweight materials prevalent in aviation require high precision and reliability during the welding process, which can be delivered through the focused beam of the 3000W device. This ability to join materials without compromising their structural integrity is crucial for maintaining safety and performance standards in aircraft manufacturing.
In the construction field, the applications of handheld laser welders extend to both structural steel and metal roofing installations. The rapid and efficient operation of the 3000W handheld laser welder enables contractors to achieve quick turnarounds on projects, enhancing overall job productivity. Its portability also allows for ease of use in difficult-to-reach areas, making it an essential tool for modern construction practices.
Beyond industrial applications, this innovative welding technology has made significant strides in artistic metalworking. Artists and designers appreciate the ability to create intricate designs and unique pieces without the constraints of traditional welding methods. The handheld laser welder’s precision allows for the fabrication of delicate pieces that highlight craftsmanship while maintaining structural stability, thus bridging the gap between artistry and engineering.
Overall, the 3000W handheld laser welder showcases its versatility through its effective utilization across automotive, aerospace, construction, and artistic domains, establishing itself as a revolutionary tool in the metal fabrication industry.
Technical Specifications and Operational Guidelines
The 3000W 2 in 1 Laser Welder is an advanced piece of equipment that integrates the latest technologies in metal fabrication. This welder operates on a voltage range of 220V, which is essential for providing the necessary power output while maintaining efficiency. Additionally, it boasts a power consumption of approximately 4.5 kW. This ensures that the welder can handle a variety of tasks including welding and cutting different types of metals, making it a versatile tool for professionals in the field.
Safety is paramount when using the 3000W 2 in 1 Laser Welder. This device is equipped with an array of safety features, including an automatic shut-off function that activates in case of overheating or power fluctuation. Furthermore, the welder has an integrated cooling system, which helps maintain an optimal operating temperature, thereby prolonging the lifespan of the equipment. Users are also provided with protective eyewear and gloves, which are essential when operating high-powered laser tools to protect against any potential hazards associated with laser exposure.
When operating the 3000W 2 in 1 Laser Welder, it is crucial for users to follow specific operational guidelines to maximize performance and maintain safety. First and foremost, ensure that the work area is well-ventilated and free from any flammable materials. Before starting, check all connections and ensure the device is grounded properly. During operation, maintain a steady hand and a consistent speed to achieve quality welds. Additionally, periodic maintenance checks should be performed to ensure the laser optics are clean and functioning correctly, which will contribute to enhanced precision and finish quality in projects.
By adhering to these technical specifications and operational guidelines, users can optimize the functionality and durability of the 3000W 2 in 1 Laser Welder, standing out as a reliable tool in the metal fabrication industry.
Maintenance and Troubleshooting Tips
Maintaining the 3000W 2 in 1 Laser Welder is crucial for extending its lifespan and ensuring efficient performance. Regular maintenance not only enhances the welder’s reliability but also reduces the likelihood of unexpected breakdowns. One of the first steps in maintaining the laser welder involves routine cleaning. Operators should regularly inspect and clean the focusing lens and the internal components to remove any accumulated dust or debris. This cleaning can be performed using a soft cloth and a suitable lens cleaner. Additionally, ensuring that the fan and cooling system are functioning correctly is vital for preventing overheating, which can damage sensitive components.
Another essential maintenance task is to check the gas supply. The 3000W laser welder operates efficiently with appropriate gas pressure, typically helping in maintaining a stable and concentrated beam. Operators should ensure that there are no leaks in the gas system and that the gas tank is adequately filled to avoid interruptions during usage. Furthermore, inspecting and tightening any loose connections in the electrical wiring can help maintain optimal performance.
In case operators encounter issues while using the welder, a few common troubleshooting steps can be beneficial. For example, if the laser is not producing any output, one should check the power supply and ensure that the device is powered on. If the beam appears weak, it’s essential to examine the settings, as incorrect parameters can lead to insufficient energy delivery. Notably, if the focus is off, adjusting the focal length as per the manufacturer’s guidelines can resolve the issue. By keeping up with these maintenance tasks and troubleshooting practices, operators can ensure that the 3000W laser welder continues to operate at its best, enhancing both productivity and safety in metal fabrication processes.
Customer Reviews and Feedback
The 3000W 2-in-1 handheld laser welder has garnered attention in the metal fabrication industry due to its impressive performance and versatile applications. User reviews highlight a mix of experiences, showcasing both commendations and criticisms that provide insights into its practical use in various settings.
Many users express satisfaction with the welder’s efficiency, noting that it significantly reduces fabrication time compared to traditional welding methods. One user mentioned that the lightweight design and portability allowed them to maneuver easily in tight spaces, making it ideal for on-site repairs and projects. Positive feedback also often centers around its dual functionality as both a welder and cutter, enabling flexibility for diverse metalworking tasks. Additionally, a significant number of reviews praise the precise control this equipment offers, which results in clean, high-quality welds without distortion.
However, not all experiences have been positive. Some users have voiced concerns regarding the learning curve associated with mastering the handheld laser welder. Initial adjustments to settings and techniques can be intimidating for novices, leading to frustration when attempting to achieve optimal results. Moreover, a few reviews pointed out that the device’s cooling mechanism could be improved, as it sometimes overheats during extended use. This feedback suggests that while the product excels in performance, it could benefit from enhancements to user experience and durability under heavy workloads.
Overall, the aggregation of customer feedback illustrates that the 3000W handheld laser welder has substantial merit in the field of metal fabrication. The varying user experiences highlight important aspects of the product, enabling potential buyers to make informed decisions. Continued improvements based on user suggestions may further enhance its reputation among professionals.
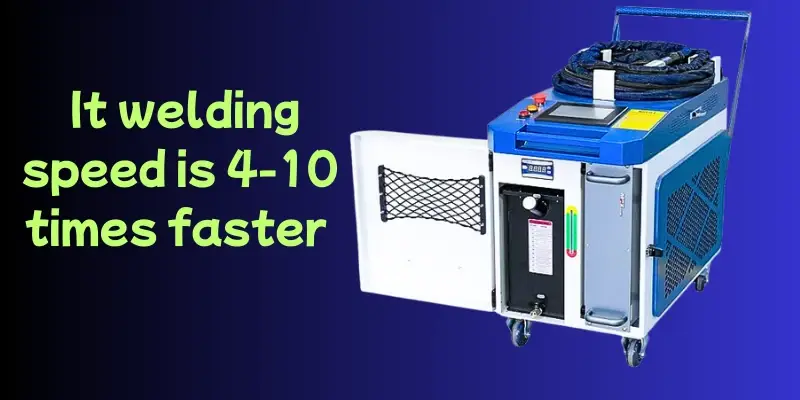
Conclusion and Future Trends in Laser Welding
Throughout this exploration of the 3000W 2-in-1 handheld laser welder, we have highlighted its transformative role in modern metal fabrication. This innovative tool not only streamlines the welding process but also enhances accuracy and efficiency, making it a valuable asset for contemporary production environments. The ability to switch between welding and cutting functions further establishes its versatility, catering to a variety of metalworking needs.
Looking ahead, the future of laser welding technology appears promising, with several significant trends emerging that could shape the landscape of metal fabrication. One of these trends is the ongoing miniaturization of laser welding equipment, which allows for greater portability and accessibility. As this technology becomes more compact, it opens opportunities for welder-operated applications in confined or complex environments. Furthermore, advancements in fiber laser technology are expected to further improve the power and efficiency of laser welders, resulting in even higher quality welds.
Automation and integration with digital systems is another crucial trend gaining traction within the industry. As manufacturing processes increasingly adopt smart technologies, the integration of laser welding equipment with robotics and AI-driven systems can yield significant improvements in precision and repeatability. This not only reduces human error but also enhances production speeds, contributing to overall operational efficiency.
Additionally, sustainability is becoming a focal point in metal fabrication practices. Future innovations in laser welding may involve the development of eco-friendly processes and materials that minimize waste and energy consumption. As environmental considerations take precedence, the laser welding industry is likely to respond with solutions that meet these challenges effectively.